引言
大直徑盾構開挖面直徑大、進排漿量大,盾構施工穿越土層及砂層時,地質環境復雜。為了確保盾構開挖面的穩定、沿線環境的安全以及盾構順利掘進,需要對泥水進行分離處理,控制泥漿指標。泥水盾構在細顆粒地層掘進時,放棄直排、沉淀固化,通過離心或壓濾等固控設備處理廢棄漿液,是目前大直徑泥水盾構施工中常見可行的一種方式。對泥水盾構泥漿配制進行了調研,提出將黏粒含量作為泥水盾構在砂層中施工時泥漿調整的一個重要指標;通過“分篩+泥水分離”組合工藝對盾構施工中產生的盾構渣土進行減量化、資源化、無害化處理,減小了盾構渣土的體積和含水率;以廣深港客運專線泥水盾構施工德國沙堡泥水分離設備為例,對泥水的分離處理進行系統論述,介紹了泥水平衡盾構施工中泥水分離設備在復雜地層中的常見問題及處理方法;以新建京張高鐵清華園隧道為背景,采用泥漿環保綜合處理的方法,提出以泥水分離設備為核心,對泥漿進行總體處理,合格的泥漿再利用,不合格的棄漿則通過分離設備和化學藥品進行環保處理,降低盾構施工對環境的影響;以福州地鐵2號線厚庭站—桔園洲站區間工程為例,通過對常規泥水處理系統及配套設施進行優化和改進,從而改善泥漿處理系統及配套設施占地面積大、處理效率低、循環利用率低等問題;介紹了泥水盾構新舊泥漿交替補充,新漿的制備、舊漿的處理,通過泥水分離系統和制調漿系統,滿足盾構施工需求,節約資源、減少外排。分別介紹了泥水盾構泥水循環模式、泥漿施工應用、泥膜、廢棄泥漿運輸、廢棄泥漿固化等盾構施工狀況。目前國內針對大直徑盾構泥水處理的研究,主要集中在通過分離設備如何減少廢漿排放上,但離心機或壓濾機產生的液相物料中,含有的化學藥品等固相物料,排放時還是會對環境造成一定的影響。關于如何將離心和壓濾處理2種方式有機結合起來,來控制泥漿指標(密度、黏度等),實現大直徑盾構掘進施工時泥水循環系統的動態平衡(不排放廢漿和液相物料),目前研究較少。本文以京沈客運專線13標望京隧道工程為研究背景,著重介紹離心機泥水處理技術和壓濾機泥水處理技術,最后對2種處理技術進行分析并總結其在工程中的應用。
1 工程概況
北京至沈陽鐵路客運專線(以下簡稱京沈客運專線)北京段站前工程(不含動車運用所)13標 位于北京市朝陽區境內,線路起點位于崔各莊鄉草場地村,緊鄰京包鐵路(鐵路東側),線路呈南北走向,標段重點工程望京隧道自草場地北側1號井始發進入地下,下穿長建駕校、南皋路、北小河、機場輔路、機場高速公路、機場快軌、京密路、來廣營東路、從馬泉營西路西側苗圃林地中2號井接收。望京隧道為雙洞單線隧道。盾構隧道采用單層管片式襯砌結構,厚度為500mm,采用C50高性能混凝土,楔形量按曲線半徑2500m圓曲線計算,襯砌全環分為6+2+1模式,管片寬度為2000mm,隧道內徑為9500mm。京沈客運專線13標使用2臺泥水盾構,盾構開挖直徑為10.9m,從1號豎井始發,2號豎井接收,盾構掘進長度為3740m。地勘資料顯示,盾構區間里程段,穿越地層主要是粉質黏土、黏土、粉土為主,砂含量較少,地層中含有大量細顆粒,直徑小于75μm的顆粒占到50%以上。
2 離心機泥水處理技術
2.1 離心方式泥水處理原理簡介離心方式泥水處理主要通過離心機、外加劑及其配套設備完成。離心機的工作原理是將處理的懸浮液(泥漿)置于增加的“離心力”作用場下,增加懸浮液體中固相物料的沉降速度。轉鼓產生高離心力,將游離液體和較細固體流向離心機較大的一端,液相物料通過溢流堰排出;較大的固相物料沉降在轉鼓壁上,形成1層泥餅層,這些泥餅由螺旋推出。
2.2 離心機設備基本參數
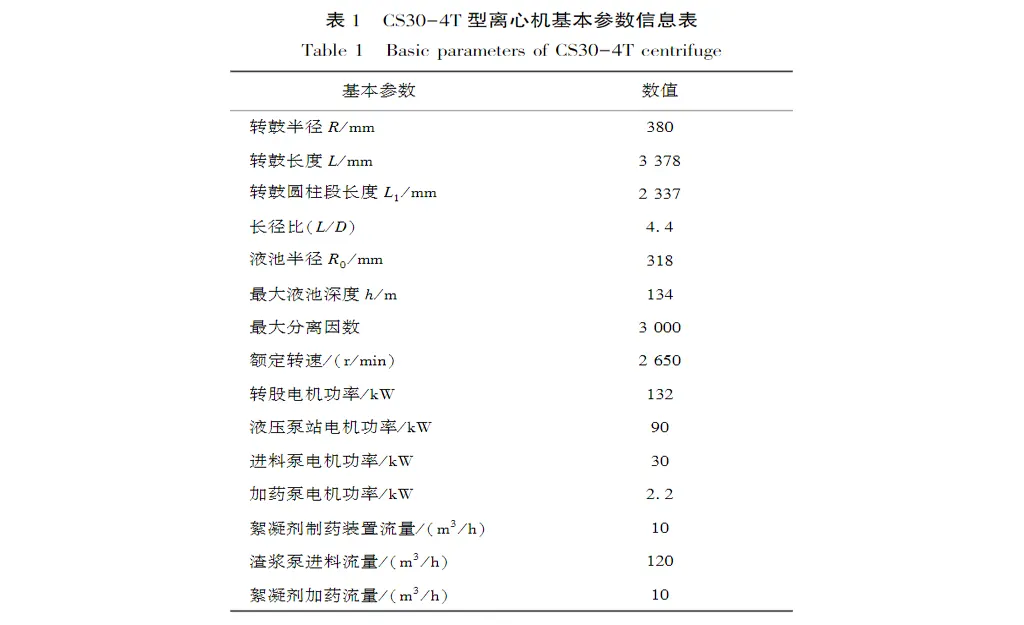
2.3 使用過程中實測參數在砂層時,離心機處理效果見表。
2.4 離心機處理能力與影響因素
1)轉鼓轉速。提高轉鼓轉速,分離因素上升,物料離心力增加,懸浮物分離得越徹底,分離效果越好,轉速的調節一般根據實際情況進行。過高的轉速會導致分離排泥不暢,壓力過高報警,以及加大離心機的磨損。考慮盾構掘進時泥漿循環利用,設定理想的轉速要根據泥漿指標而定(溫度、黏度、密度、粒度)。進料量加大,離心機的振動和噪音相對增加,設備的使用壽命也會降低。一般在滿足泥漿指標控制目標的情況下,選用最小,使清液懸浮物符合泥漿循環利用標準。
2)螺旋和轉鼓差速Δn。沉渣在轉鼓內的軸向移動依靠螺旋與轉鼓的相對運動,即Δn實現。 Δn小,螺旋對流體擾動小,分離效果好,固相沉渣在干燥區停留時間長,濾餅的含固率高,但離心機的排渣能力下降,不易排料;Δn大,螺旋對流體的擾動大,分離效果差,固相沉渣在轉鼓的停留時間短,濾餅的含固率降低,但離心機排渣能力增加。螺旋和轉鼓差速Δn,一般根據所需物料的含固率的大小而定。實驗過程中,盾構在砂層掘進時,離心機的含固率要比在黏土層掘進時大。為了便于分離的渣土外運,處理黏土層掘進時的泥漿時需適當減小Δn,相應地泥水分離時間也會延長(參見表2和表3“時間”)。螺旋推料器所產生的轉矩是衡量沉渣在轉鼓內的多少、密度及含固率。測定同一性質的物料、同樣流量、設定不同的轉矩,所產生排出濾餅的含固率不一樣,轉矩越高濾餅的含固率就越高。轉矩與Δn是相輔相成的關系,實際轉矩超過設定的轉矩,Δn就會相應增大,當轉矩恒定至設定轉矩,Δn就會恢復到設定的最小差速,Δn是隨轉矩的變化自動調節的。
3)溢流板直徑D。調節轉鼓大端溢流板直徑大小,可改變轉鼓沉降區和干燥區的有效長度,D小,液池深,沉降區增大,干燥區小,清液懸浮物減小,但濾餅的含固率降低;D大,則液池淺,沉降區減小,干燥區增大,清液懸浮物增加,濾餅含固率提高。濾餅含固率的高低通常根據工藝控制目標參數調節,調節轉鼓大端溢流板直徑的大小時必須停機。
4)進料量。進料除與離心機性能(即轉鼓轉速、差速、壓強、溢流板直徑和最大處理能力)有關外,還與控制目標清液的懸浮物指標、濾餅的含固率及物料性質有關。試驗過程中,在不改變離心機運行參數的情況下,盾構在砂層掘進時,離心機的進料量要比在黏土層時要大(參見表2和表3“進漿量”)。
5)泥餅含固率。根據加速度體積按比例增加的情況(脫水處理量與固料負載率的比例),如果增加固料負載(在進料含固率保持不變的情況下,進料流量增加),泥餅含固率將會降低。這樣,向離心機供入多余的處理量將獲得較差的泥餅含固率。離心機運行較高的流量時,將使泥餅含固率較低,如果要彌補含固率差異,就需要增加適量的絮凝劑劑量,增加離心力,或降低回收率。物料性質不同,泥漿細顆粒成分不同,所需的絮凝劑劑量也不同。盾構在黏土層掘進時,離心機絮凝劑劑量要比在砂層掘進時大(參見表2和表3“進藥量”)。
6)回收率?;瘜W調理是回收率的一個首要因素。對于高含固率離心機來說,基本上沒有什么問題,因為較低的流量已經將含固率優化在最高值范圍附近。要使離心機處理更多的物料,可能需要更換使用的絮凝劑類型或者需要添加適量的絮凝劑。絮凝劑存在過量的情況,假如過量,不是降低含固率就是使結果更差,即泥餅含固率隨絮凝劑劑量變化而變化的平面圖曲線呈S形。在過量的情況下,增加絮凝劑或者沒有影響,或者情況更差。較小離心機處理較高處理量,成本曲線向過量條件偏移得更多。如果污泥含固率發生常規變化,在過量或不過量條件下波動,清液中的固料會更高,浪費成本。泥水盾構掘進在黏土以及砂層中循環出的泥漿含量不一樣,經過泥水分離設備篩分、旋流處理后,黏土層排出的泥漿密度比砂層中掘進排出的泥漿會高很多,離心機在處理黏土層和砂層的泥漿時就產生了不同的效果。不管黏土層還是砂層,泵送到離心機的泥漿密度越高,在離心機工作時就需要加入更多劑量的絮凝劑;而且當泥漿密度較高時,離心機的處理能力也是有限度的,需要適當地降低離心機的進漿量來提高離心機的處理效果(降低渣土含水率),并且離心機泥水分離的時間也會相應增加。從表2和表3可以看出,離心機泥水分離能力隨著密度的升高而下降,藥劑消耗更大,循環時間更長。
3 壓濾機泥水處理
3.1 壓濾方式泥水處理原理簡介壓濾方式泥水處理主要通過壓濾機、外加劑及其配套設備完成,壓濾機過濾部分由整齊排列在主梁上的隔膜濾板、廂式濾板和夾在它們之間的濾布所組成。過濾開始時,濾漿在進料泵的推動下,經止推板和壓緊板的進料口進入各濾室內,濾漿借助進料泵產生的壓力進行固液分離,濾液由排液口排出。壓濾機工作原理見圖2。
3.2 壓濾機設備基本參數 壓濾機基本參數信息見表4
3.3 使用過程中實測參數砂層掘進時壓濾機泥漿處理效果統計參數見表5。黏土層掘進時壓濾機泥漿處理效果統計參數見表6。
入料密度為1.1~1.2g/cm3時,壓濾系統每h平均處理泥漿31.5m3,濾餅含水率約30%,每h平均產出干渣7.2m3,濾液含固率小于2g/L,可以直接外排或循環使用。壓濾設備每min能生產約0.1m3干渣,即生產1m3干渣土約需要10min。入料密度為1.22~1.36g /cm3時,壓濾系統每h平均處理泥漿約44m3,濾餅含水率約30%,每h平均產出干渣約9m3,處理效果比泥漿密度低于1.2g/cm3好。
3.4 壓濾機其他添加劑試驗情況
1)添加劑采用聚合氯化鋁,泥漿密度為1. 17g/cm3,添加量參考石灰添加量下料,石灰平均每h處理30m3泥漿,聚合氯化鋁平均每h處理40m3泥漿。濾液水pH值為8,3板的含水量分別為26.8%、31.9%、36.8%,平均含水量約30%。效果最好的1板入料循環時間為4000s,擠壓時間為1000s,餅厚為4cm。
2)添加劑采用石膏,泥漿處理量跟石灰差不多,平均為30m3/h。壓了2板,濾液水pH值都是8,2板的含水量分別為24.2%、28.6%,平 均含水量約26%。入料循環時間為4000s,擠壓時間為800s,餅厚為4cm。
3)添加劑采用鋁粉,泥漿密度為1. 18g/cm3,鋁粉與水,與漿液有反應,有氣泡,透水性不好,和沒有添加劑效果一樣。
4)添加劑采用鋁粉與石膏混合,泥漿密度為1.15g/cm3,每板加100kg石膏粉和8kg鋁粉,處理效果與只添加石膏粉差不多,鋁粉加入后,液面會起1層氣泡,鋁粉引起的氣泡長時間不破,效果不如只添加石膏。
5)添加劑采用鋁粉與石灰,密度為1. 16g/cm3,每板加100kg石灰,8kg鋁粉,處理效果不佳,不成餅,效果不如只添加石灰。
6)壓濾機進漿處增加旋流器(10μ m),由于泥漿已經由泥水分離設備二級旋流、篩分處理過,壓濾機處增加的旋流器提濃效果不明顯,只能采取多次旋流的方式來提高泥漿密度。壓濾機進料密度能增加約0.05g/cm3,效 率低且能耗大。
3.5 壓濾機處理能力與影響因素由3.4節分析可知:
1)壓濾方式泥水處理在泥水密度較大時效果更明顯,添加劑采用聚合氯化鋁時,比其他添加劑效果更好;2)濾板的不同,添加藥劑的數量不相同,壓濾系統的處理能力也不盡相同。
4 泥水處理效能分析離心機在泥漿密度為1.19g/cm3時 處理能力約為60m3/h,產生干渣量為0. 2m3/min(含水率約60%),液相物料(廢水)含固率高。壓濾機在泥漿密度為1.29g/cm3及 以上時,處理效果最佳,處理量約為30m3/h,產生干渣量為0. 1m3/min(含水率約30%),液相物料含固率低。 2種泥水處理分離方式在項目實際應用效果見表7。
由表7可以看出:盾構掘進1環,掘進后沉淀池泥漿密度由1.16g /cm3變為1.22g/cm3,上 升了0.06g/m3,黏度上升了0.78s。經振動預分篩、2次旋流器處理(一級旋流器、二級旋流器)、迷宮式沉淀池三級沉淀后密度為1.19g/cm3,只 降低了0.03g/m3,且20μm以下細顆粒分離難度大,此時需要采用離心機或壓濾機對沉淀池的泥漿進一步處理。泥水處理工廠流程見圖3。
三級沉淀后的泥漿,經離心機處理(液相物料排放至調整池)、壓濾機處理(液相物料排放至清水池補充進排漿泵站密封水損失)調整后開始下一個掘進循環。盾構掘進結束時調整池的密度為1.19g/cm3,通過離心、壓濾處理后,密度降低了0.03g/m3,調整池的密度降低到1.16g/cm3,達到上一循環開始掘進時的狀態,泥水處理工廠達到動態平衡的狀態,既不需要往外排漿(不產生廢漿),也不需要向調整池和進漿池加水或新鮮漿液降低泥漿密度,實現了大直徑泥水盾構施工“零排放、零污染”的目標。
5 結論與討論目前,大部分泥水盾構施工,主要著重于廢漿處理及產生的液相物料(廢水)達到市政排放標準方面,對不產生廢漿或不向外排放液相物料的研究較少。本文以京沈客運專線13標泥水處理工廠為依托,研究如何實現泥水循環系統動態平衡。主要結論如下:
1)離心方式處理泥漿時,可以通過調整離心機參數及外加劑參量,控制排放液的流量和含固率,并排放至調整池改善泥漿密度(泥漿密度高時開挖掘進困難,密度過低時循環攜渣困難)。
2)壓濾方式處理泥漿時,受外加劑影響較大,泥水處理效率沒有離心機快,但產生的干渣和排放液效果比離心機好,且能分離泥漿中的膨潤土等制漿材料,調整泥漿黏度,排放液可以當密封水、冷卻水循環使用,控制泥水處理工廠液相物料向市政管路外排。3)合理選擇泥水分離處理設備,優化組合,可以實現大直徑盾構泥漿處理“零排放”的目標。針對泥水分離設備尋找新型外加化學藥品,進一步提高處理效率、節約成本、保護環境。
聲明:本文章版權歸原作者及原出處所有。
歡迎來電咨詢、技術交流、來料實驗。